This article is about the selection of materials for the design and production phases for different production sectors and especially about pharma. Further continues with the general requirements of plastics for pharma applications. It also explains a few reasons for plastics are to be used in pharma and what factors affecting the pharma industrial packaging sector to increase its market size by 70% by the end of 2027.
By Anantha Sairam Pasupulati, Cademix Institute of Technology
Selection of Material
Material is a substance or mixture of substances that make up an object. Materials can be pure or impure, living or non-living. Materials are classified as per physical and chemical properties, as well as their geological origin or biological function. Hundred types of materials As per the Year. There were no synthetic polymers back then; now there are over 45,000 of them. There were no high-performance composites available before; now, there are hundreds of Selection of material.
There are so many types of materials available in the market but here we talk about Plastics and their applications in the pharma industry. Researching a specific plastic, a material-technical datasheet can be a good place to start, but it has limitations because it only provides a snapshot of selected data.
Although this is a useful method for comparing test data and assessing the quality of incoming materials, a material selector should be aware of other factors to consider. For example, thermoplastic materials have viscoelastic nature, and based on time, temperature, and stress long-term performance will be influenced. (1)
Here article focuses on the selection of materials based on different perspectives and different stages that undergo any production unit.
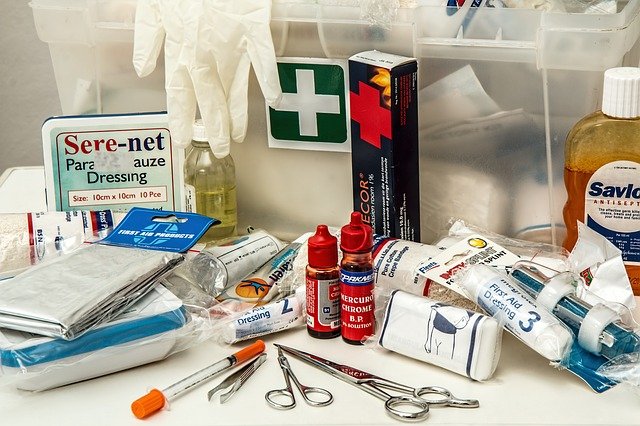
1: Based on Product Design requirements (2)
Why Pharma Industries Focusing on Plastics
The Packing materials are PETPolyvinyl chloride (PVC), polypropylene (PP), polycarbonate (PC), high impact polystyrene (HIPS), polyethylene terephthalate (PET), and high-density polyethylene. Plastics are easy to shape and size, have protective properties, and are inexpensive, making them an excellent choice for pharmaceutical packaging. These plastics protect drugs from physical damage and contamination. Its applications, including bottles, closures, blister packs, jars and canisters, and overwrap. (4)
General Requirements for Plastics in Pharmaceutical Engineering
What are the most common plastics needs in pharmaceutical plant engineering?
There is no simple answer to this question. GMP regulations partially exclude this topic, and there is no “gold standard” either. Based on specific applications new requirements are determined.
Elastomers, soft plastics (such as foil), and hard plastics (such as valve bodies) are all used (e.g. membranes for membrane valves or o-rings). Surface finishing and material compatibility are important quality characteristics. (5)
Surface finishing
The surface of plastics is more difficult to determine. Mechanical detectors do, in fact, risk scratching the plastic surface.
Statistical methods are used to find the average roughness of a plastic material. Roughness-tested samples are thrown away to avoid scratch surfaces in real-time applications. Non-contact measurement methods, on the other hand, have the potential to be used (e.g. white light scanning).
The manufacturing process generally ensures high surface quality in the case of thermoplastics produced by injection molding and for which manufacturers use highly polished injection molds. Surface roughness that is significantly better than stainless steel Ra values (e.g. = 0.8 m) can be achieved here. This is also confirmed in material certificates, and if the supplier’s quality system is regarded as reliable, it can be considered adequate.
Material compatibility
Because plastics are composed of organic substances and thus are not completely inert, the first step is to ensure that the container is stable in front of the cosmetic product. This appearance must ensure that, on the one hand, the product does not react chemically with the container and, on the other hand, the container does not undergo any changes, such as deformations, collapse, and so on. (6)
The most basic GMP requirement is that the plant material has no negative impact on the pharmaceutical product’s quality. A certificate of food suitability is frequently used as proof that a substance is not toxic when consumed in small amounts.
- “US Federal Standard known as CFR 21.177
- The positive list of the Federal Institute for Risk Assessment “Recommendations on Materials for Food Contact” (formerly “Plastics Recommendations; Health Safety Food, Commodities and feed stuffs Code” (LFGB))
- EC1935/2004 (When materials and/or articles supposed to come into contact with food)
- EC2023/2006 (Good manufacturing practice for materials and articles intended to come into contact with food).
It may however be useful to provide specifications, for further compliance with other requirements:
- 3A Sanitary Standard
- EHEDG (European Hygienic Engineering & Design Group)
- DIN 26055 – hose assemblies or use in the pharmaceutical and biotechnical industry
- DIN ISO 3601-3 Form and surface deviations of o-rings (for pharmaceuticals, observe “Grade characteristic S”)” (5)
Recently the big pharma industries use plastics especially in the field of packaging. Here we do little focus on Ideal plastics for packaging
Qualities of an ideal plastic container
It’s critical to understand the plastic’s entire manufacturing formula, including all additives used during the manufacturing process, when selecting a plastic container for a pharmaceutical formulation. This enables the formulation scientist to identify and eliminate potential hazards, ensuring that the packaging system is suitable for its intended use. In the pharmaceutical industry, plastic containers should be designed in such a way that: The ingredients are not significantly adsorbed on the surface of the plastic package or absorbed into or through the plastic container when the formulation comes into contact with it.
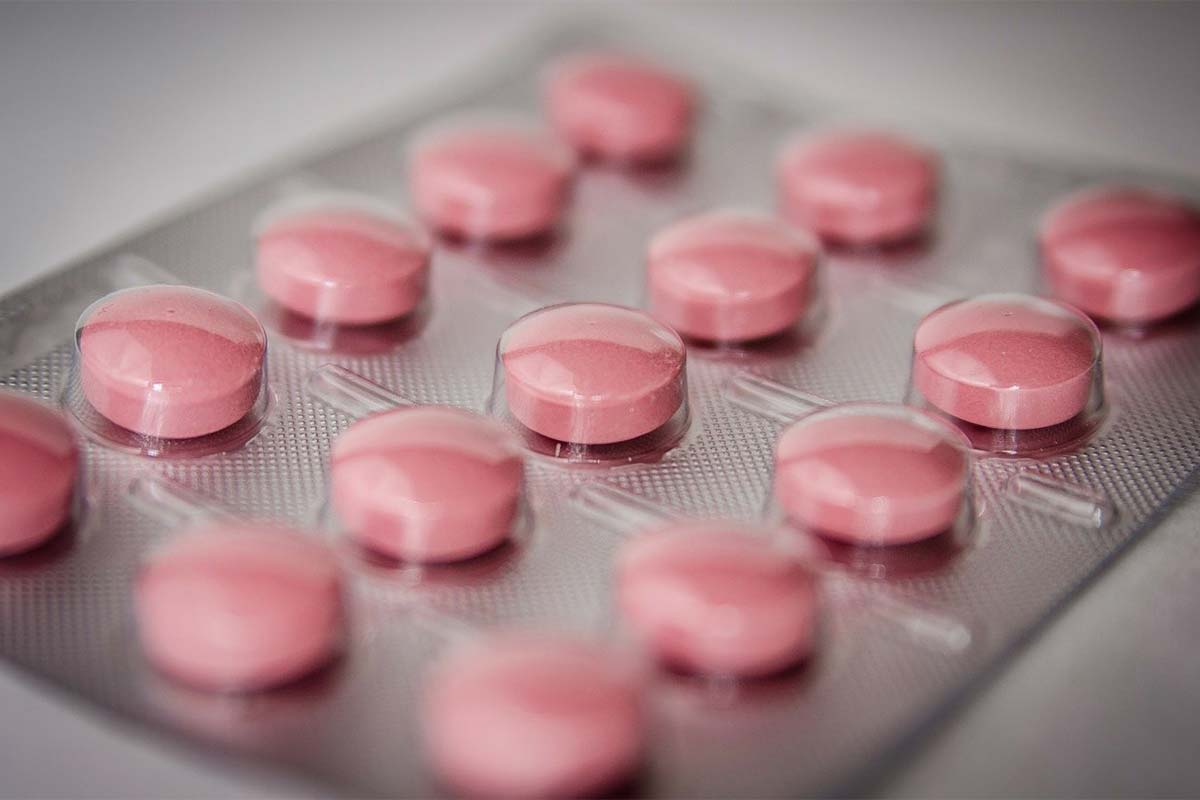
Due to the release of substances (leaching of plastic materials) in sufficient quantities into the formulation, the plastic package has no effect on the formulation’s stability. (7)
Factors Affecting the Increase of the Pharma Packaging Industry
By the end of 2027 companies are expecting to increase their market size up to 70% of today’s market size. From Fortune Business Insights let’s see what factors affect them to increase their business.
- Latest trends: Recently pharmaceutical packaging demand has increased as a result of the development of novel drug packaging systems. Because they are used in the onetime application process and they are quite suitable for the injections like vaccines.
- Driving trends:
- Rising population, increasing technological innovations, increased healthcare awareness, adoption of advanced manufacturing processes, increased spending in public healthcare systems, and government implementation of new regulations to control the spread of infectious diseases are all contributing factors to the growth.
- Many businesses are investing in the production of generic drugs in order to provide medical treatments at a lower cost. This novel packaging is critical in the manufacturing of generic drugs. So it can protect drugs during storage and transportation. As a result, rising demand for generic drugs will drive up prices.
- Regional Insight: Europe is the market’s second-largest region, with the leading countries being Germany, the United Kingdom, and Italy. Now the region’s growth is attributed to the increasing use of pharmaceutical products such as plastic bottles and containers, vials and ampoules, and pre-fillable syringes. Furthermore, the market’s lucrative growth has been fueled by governments’ increasing adoption of new regulations to control the spread of infectious diseases, such as COVID-19. (4)
Conclusion
The material has developed exponentially in the last two centuries. Should not violate the international standards for creating new material or developing existing material. create a set of selecting materials by using requirements and different flow charts. The final selection of material can be done by the selected materials and comparing them with the requirements of the pharma industry. After going through the business insight finally, it can be concluded that usage of plastics in the pharmaceutical industries is also increasing exponentially.
Bibliography
1. Ashby, Mike. Materials. United States: Elsevier Ltd, 2019. ISBN: 978-0-08-102376-1.
2. Pfeifer, Michael. Selecting Materials. s.l. : Elsevier’s, 2009. ISBN 13: 978-0-7506-8287-9.
3. Scallan, Peter. Process Planning || Material evaluation and process selection. Oxford : Elsevier, 2003. ISBN 0 7506 5129 6.
4. Packaging/ Pharmacetucal packaging Market. Fortune Business Insights. [Online] https://www.fortunebusinessinsights.com/pharmaceutical-packaging-market-102860.
5. General Requirements for Plastics and Pharmaceutical Engineering. Good Manufacturring Practice. [Online] 06. 11 2019. https://www.gmp-compliance.org/gmp-news/general-requirements-for-plastics-in-pharmaceutical-engineering.
6. FARMACIA Y COSMÉTICA. Interempresas. [Online] https://www.interempresas.net/Farmacia/Articulos/103553-El-envase-plastico-en-la-industria-farmaceutica.html.
7. Plastic Containers for Pharmaceutical Use. Pharmapproach. [Online] https://www.pharmapproach.com/plastic-containers-for-pharmaceutical-use/.
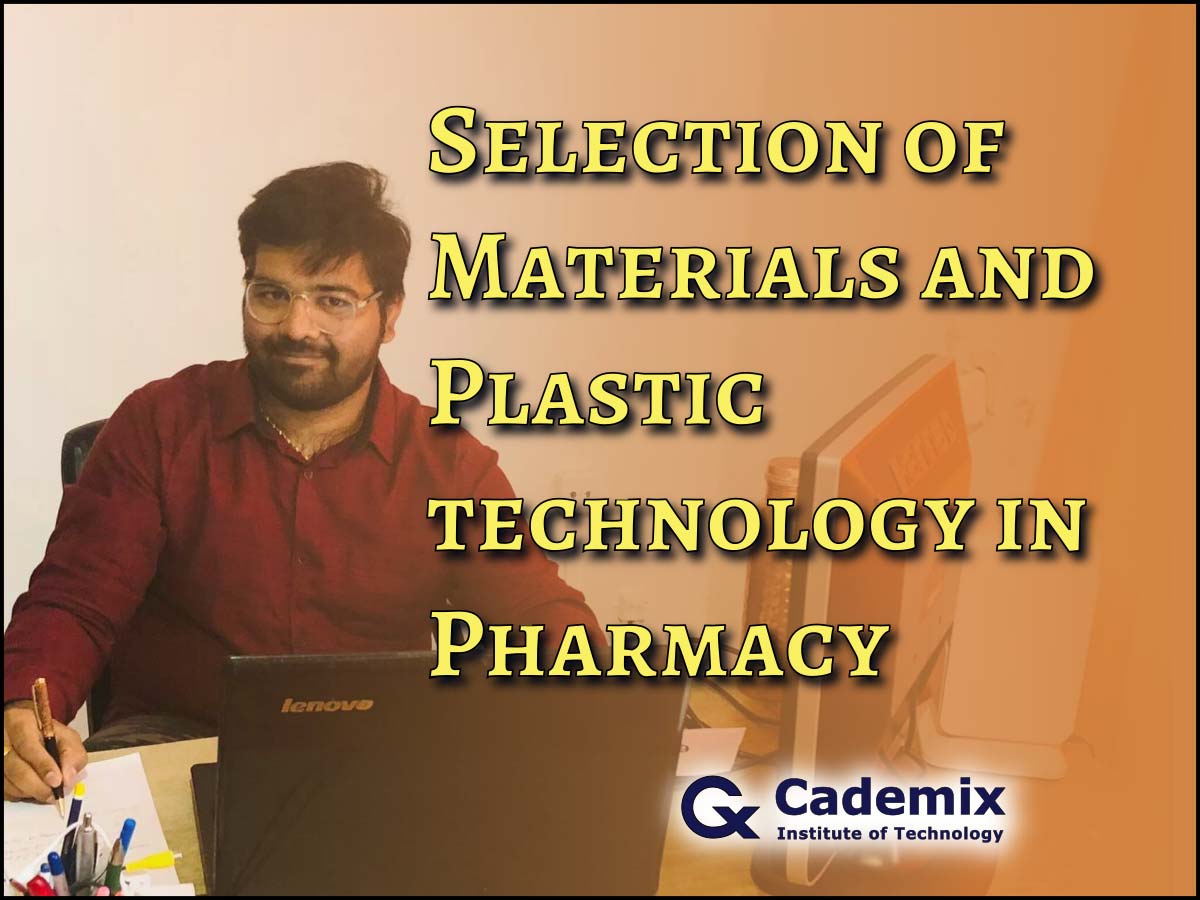
About the Author
A multidisciplinary mechanical engineer, originally from India, with legal status to work in Germany and Austria. He is graduate of Plastics and Product Refinement Engineering from the Hochschule Kaiserslautern, Germany, and an associate member at the Cademix Institute of Technology.
He has experience to optimize production and virtual verification for generative and additive manufacturing process. Has technical skills in design of 2D, 3D parts, assemble and simulation across manufacturing industry. He has experience in NDT testing and mechanics of materials. Time management, Material ordering, Material selection, sales and business communication skills, independent working, guiding, or helping fellow colleagues with their projects, Problem solving skills and highly initiative in new topics or/and projects.
Related Keywords
Pharma, Molded, Resin, HDPE, Melt, Recycled, Extrusion, Low density, Resins, Polyvinyl, Polyvinyl-chloride, Melting, Nylon, Polymerization, Tensile, Ethylene, Thermoset, Mechanical properties, Low density polyethylene, Recyclable, Chemical resistance, Fabrication, Copolymer, Tooling, Extruded, Types of plastics, Biodegradable, Monomer, Crystalline, Polyester, Amorphous, Toughness, Tensile-strength, Styrene, Blow-molding, Elastomer, Reinforced
pharmacy, pharmacist, pharmacies, pharmaceutical, clinical studies, pharmaceutical industry, pharmaceutical materials, pharma material, pharmaceutical companies, pharmaceutics, pharmaceutic materials, pharmaceutics plastics, pharmaceutics activities, pharmaceutic industry, clinical tries, clinical study, clinical materials, healthcare, hospital, tablets, pills, medicine, medical, gel capsules,