Management of required Materials, goods and spare parts for maintenance and overhaul projects in a petroleum oil refinery is the subject of this article. Here we talk especially about Spare Parts Management in overhaul projects – A Case Study in Oil Refining Companies. First, we talk about Maintenance and its various categories. Then we will briefly define overhaul projects in oil refineries. We will also focus on the management of required spare parts for overhaul projects as a special type of maintenance. After it, we will explain its mechanism.
By: Sohrab Askari (Associate Multidisciplinary Engineer at Cademix Institute of Technology, Austria)
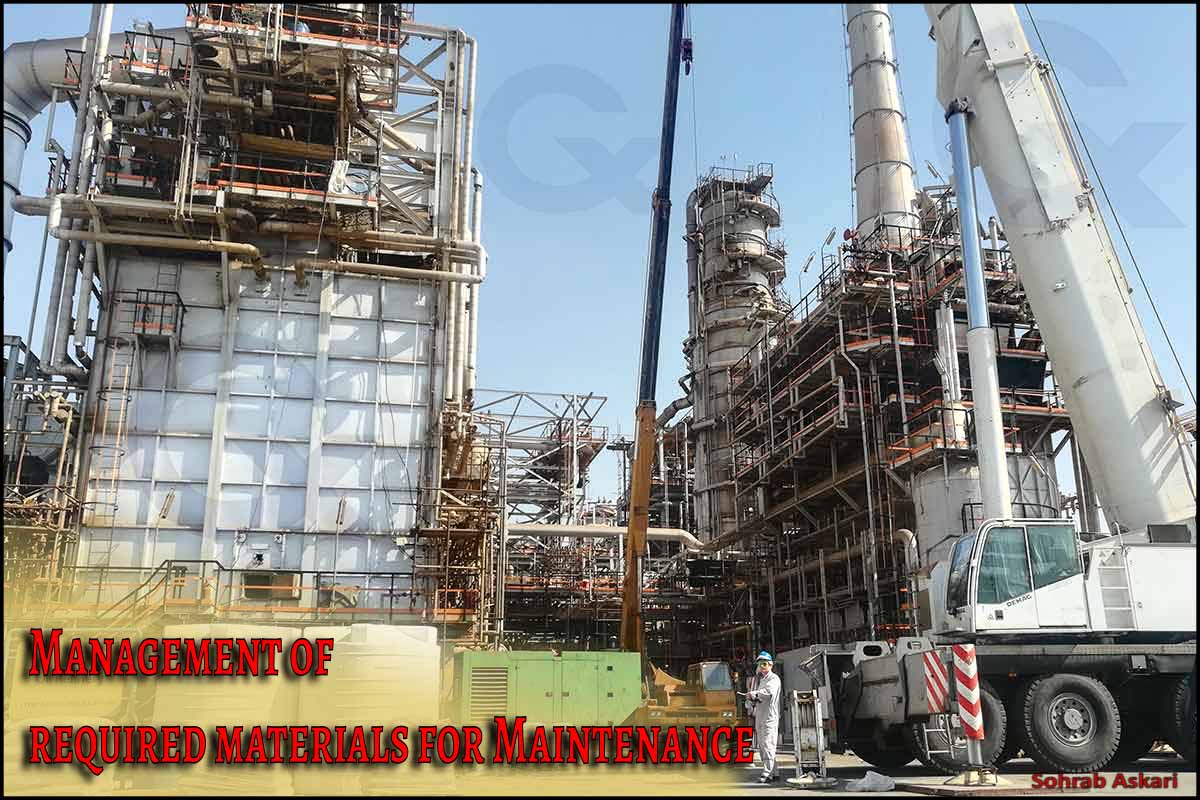
Maintenance – Definition
Maintenance means planning and performing activities on equipment that provides a continuous operational situation to produce a quality product or service. The main basis of Maintenance is the care of equipment and if necessary, repairs will be done. It is one of the most important management concepts in oil industries, especially in oil refineries.
The most Types of Maintenance
Most types of maintenance follow:
1- Corrective Maintenance (CM)
2- Preventive Maintenance (PM)
3- Predictive Maintenance (PDM)
4- Emergency Maintenance (EM)
5- Planned Maintenance (PM)
In order to avoid deviating from the main subject of the article, we will briefly explain the first four types and leave further study in this regard to respectful readers. We will examine the fifth type in more depth due to its more relationship with the main subject of the article.
1-Corrective Maintenance (CM)
This method is the replacement or repair of equipment after it fails. It was used in the past and before the Second World War. The initial cost of this method is low but it is inefficient. Also, in the long term, it is very expensive because we use it when a breakdown occurs. Perhaps this method can only be called repairs because it is used just after a failure!
2-Preventive Maintenance (PM)
we use Preventive Maintenance to prevent a breakdown in the equipment and maybe repair or care oriented. In any case, it prevents a breakdown or failure and unplanned shutdown of equipment. “PM” includes inspection, survey, checking, service, wrenching, balancing, replacement of parts, lubrication, and so on.
3- Predictive Maintenance (PDM)
PDM monitors the activity of equipment. It issues very important statistical data to determine and predict the probability of equipment failure in the future. After it, the PM unit can explain and execute preventive repair activities on the equipment at a scheduled time.
4-Emergency Maintenance (EM)
A malfunction of a device causes the stop production. We should repair it as soon as possible. Following this type of Emergency Maintenance, abbreviated as EM, we perform a set of activities mentioned in CM. The most important of them are activities to limit the spread of damage to other equipment and machinery. Then repair the device to reach the expected conditions.
5-Planned Maintenance (PM)
Planned Maintenance is a smart preventative approach that maintains equipment and machinery by a scheduled plan. It leads to avoiding the high costs of reactive maintenance. It also decreases the risk of failures. PM keeps a production unit of the oil refinery in an optimal situation.
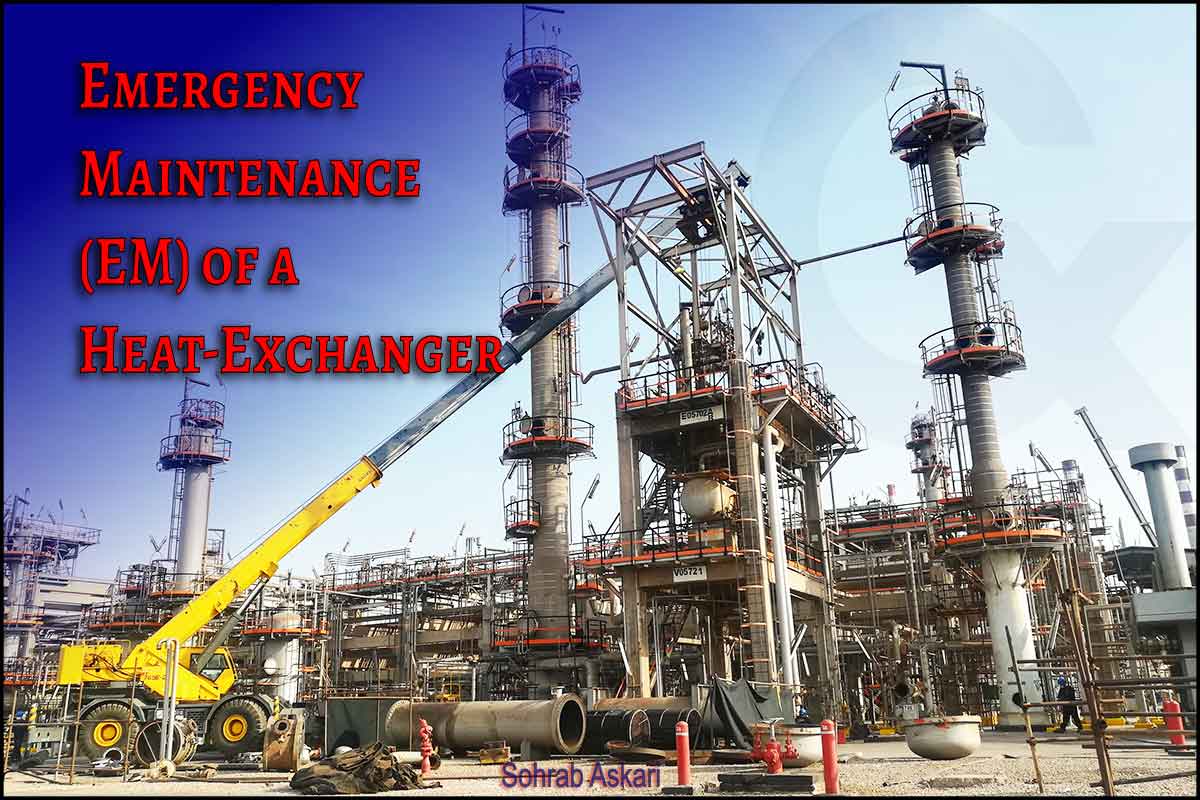
The scheduled maintenance varies depending on:
1-The type of asset being maintained
2-The environment in which the equipment operates
Some assets require frequent maintenance while others could operate for years without any failure. The more planned maintenance you perform, the longer your assets will remain operating at peak without failures! It is a general rule.
In order to build a proactive maintenance plan, oil refining companies must frequently provide the following activities:
- Materials and spare parts that might need to replace old parts.
- Needed tools for implement the maintenance.
- Human resources will need to perform the maintenance activity.
The most important of the Planned Maintenance is Overhaul. In the continuation of the article, we are going to introduce the Overhaul; then, we will study Logistics related to it.
Overhaul – Definition
An Overhaul is a frequently used word in the industry and especially in maintenance. By definition, an overhaul means a thorough checking and performing the required repairs or reparations of all machinery, equipment, and parts in an industrial unit. We use the term frequency in complex Industries including the oil production industry, aviation industry, ships and vessels, trains, airplanes, etc.
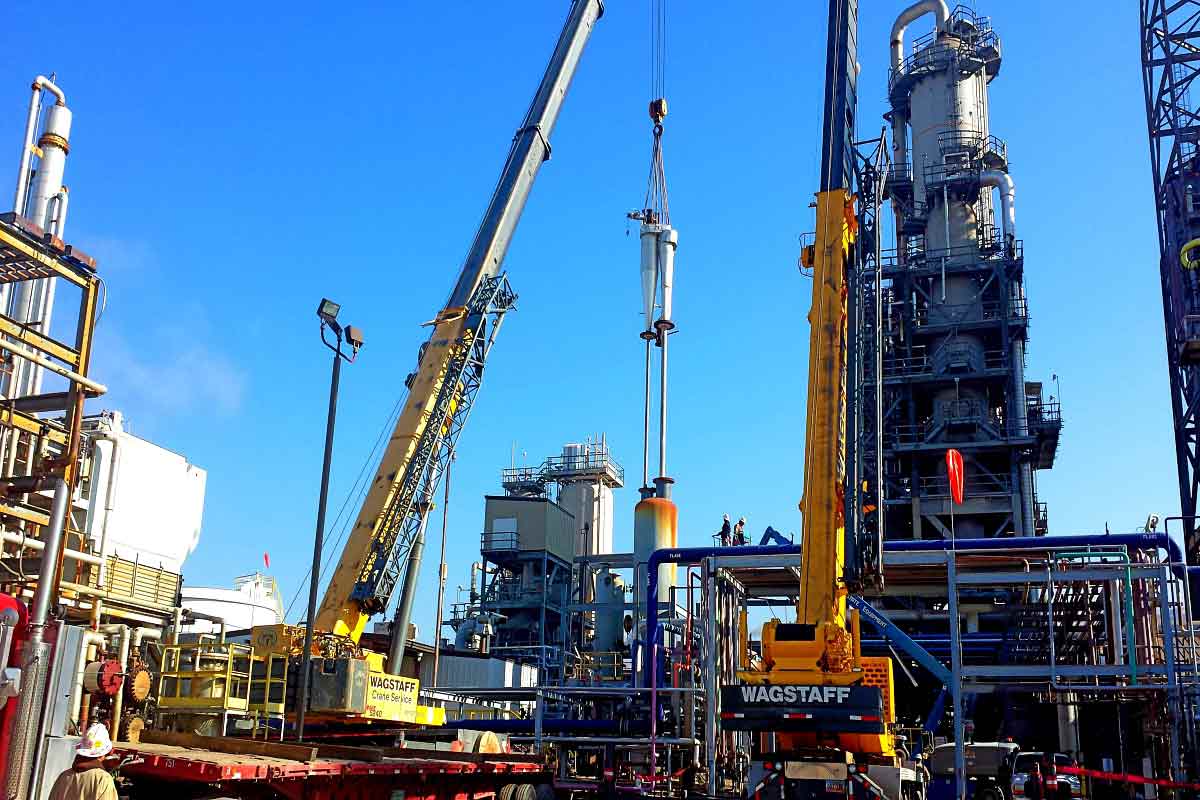
There are a large number of installations, equipment, and machinery in the refinery that are always working to refine the crude oil and produce petroleum products.
Overhaul in an Oil Refinery
Overhaul in oil refining companies is a total checking of installations, machines, and equipment and doing needed repairs. For instance, it includes distillation columns, atmospheric towers, heat exchangers, pumps, compressors, vessels, tubes, and so on.
It is worth noting that refinery overhaul projects are often carried out in two methods: Waterfall and Agile; Because we are not going to discuss the overhaul projects methodologies in this article, I would just like to draw your attention to an article by the same author with title “Agile Project Management in Refineries overhaul“.
Requirements of Spare Parts Management are Logistical Challenges in an Oil Refinery
Logistical challenges are the main concerns of maintenance management. We need Materials and spare parts for the overhaul implementation. Providing them is one of the most Logistical challenges!
Materials and Spare Parts Requirements for Overhaul Management in Refinery
The lack of some key and vital materials and spare parts is an important problem. It makes the implementation of maintenance projects (especially, overhaul projects) related to some machinery or equipment impossible! Sometimes, machinery or equipment is a very important and vital component; If you can not repair them, the whole overhaul project will be in vain! These mentioned vital components are known as “deterrent” components; The lack of such deterrent components may cause delay or cancel the whole overhaul project. Subsequently, it can impose huge risks or damage to the refinery! So, in order to implement an effective overhaul on time, we must provide the required materials and parts in time!
Logistical Challenges Related to Spare Parts Management in Refinery
The cost of stopping production in an operating unit that is going to be overhauled is very high. On the other hand, reducing warehousing costs (cost of stored capital) is very important. But If the required parts are not available, the execution of overhaul will be impossible or the duration of stopping production will increase. So, warehousing costs will not be comparable to costs of stopped production or damages!
It is so significant that the overhaul may not implement on time. But regular availability of required materials and spare parts leads to the accumulation of spare parts; Subsequently, it expends huge amounts of capital costs. So, in order to prevent encountering such a situation, Material & Spare Parts Management should focus more on service quality than parts warehousing costs. Materials & Spare Parts Management is a really so exciting subject in Maintenance & Overhaul in Refinery.
Actually, there are two incompatible subjects:
- The availability of required spare parts.
- Decreasing the cost of them accumulation!
Proper implementation of the overhaul project management cycle will not be possible without timely procurement of materials and spare parts. It needs efficient management of materials and spare parts. The unavailability of even one spare part may delay some maintenance activities. It also causes incur additional costs and increases the duration of the entire overhaul project. This, in turn, drastically increases the cost of stopping production by increasing the shutdown duration of that production unit.
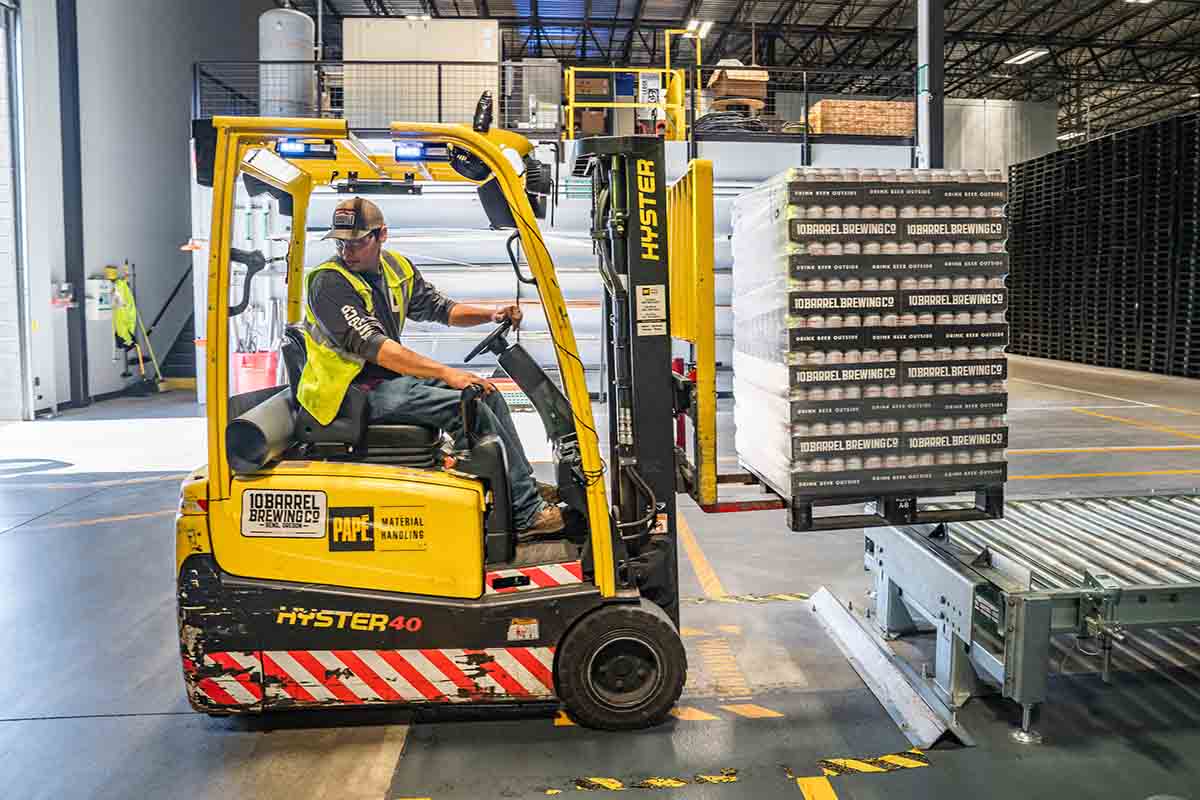
The Role of the Procurement Manager
The procurement manager plays a very key role in efficient Logistics. The process of materials and spare parts procurement and delivery for storage should be efficient. Otherwise, informal hidden warehouses or secondary warehouses will be established over time. The creation of these hidden warehouses will cause no feedback to the storemen. As this trend continues, storemen also reduce inventories based on how long the material and spare parts are in storage. The more inventory there is, the higher the warehousing costs. Also, the more likely it is that the goods will be damaged or scrapped.
These two types of incompatible reactions (unavailability of spare parts and informal hidden warehouses creation) set the stage for the fall; An event that isn’t satisfactory for anyone! Therefore, there is a really huge challenge: On the one hand, excessive investment in spare parts limits working capital, and on the other hand, if the investment be not enough, we will have trouble responding to maintenance requirements when a failure occurs!
What’s the Spare Parts Management in an Oil Refinery?
Materials and Spare Parts Management department is an important section of Maintenance Management in the refinery. It plays a vital role in solving mentioned challenges. It does that through required material planning, control, coordination, and follow-up on the supply processes. Materials and Spare Parts Management Establishes a balance between the flow of supply and consumption. Controlling the relevant processes is one of the principles of material management. Therefore, the management of the supply of required spare parts for overhaul is an integral part and inseparable element of maintenance management.
The Materials and Spare Parts Management department is basically apart from the Procurement Department. That is a vital connection bridge between Maintenance Management and Logistics Management. As one of the most important pillars of Maintenance Management, it makes Logistics Management able to answer its responsibility well. Undoubtedly, Materials and Spare Parts Management plays a vital role in the Logistics processes (and subsequently, in the SCM).
But how does it work? What sections does it have? What tools does it use? And finally, how does it balance things out? You will find the answers to these questions in the next sections of the article.
Operational Phases of Materials & Spare Parts Management, Related to Overhaul in an Oil Refinery
The main role of Materials & Spare Parts Management is the Overhaul in Refinery. In relation to overhaul, material management carries out activities in three general phases:
1- Pre-overhaul phase
2- Phase during overhaul
3- Post-overhaul phase
In the following, we will examine each of these phases.
Pre-Overhaul Phase
In this phase, Materials and Spare Parts Management performs a set of functions in a refinery. The functions are related to needs assessment and supply of all materials and parts required for overhaul.
The start time of this phase is usually immediately after the previous post-overhaul. It is according to the instructions issued by the Technical Inspection Office. It continues until the planned overhaul.
The pre-overhaul phase includes several stages that will be explained in detail, later at the end of the article.
Phase During Overhaul
In this phase, Materials and Spare Parts Management monitors all movements of stored materials and parts in the warehouse and their consumption flow.
The requested parts are issued from the warehouse according to the overhaul executor requisitions on the basis of special documents.
The Materials and Spare Parts Management controls the consistency and proportion of the parts requisitions with BOM. It also monitors the issue documents of saved material & spare parts and delivery processes.
Post-Overhaul Phase
In the post-overhaul phase, Materials & Spare Parts Management has 4 steps:
1- Data Aggregating
In this step, Material & Spare Parts Management aggregates the gathered information of consumptions.
2- Technical Analysis
It performs relevant technical analysis on that aggregated information.
3- Technical and Managerial Reports Issue
The third step, according to quantitative and capital value indicators, prepares technical and managerial quantitative and qualitative reports. The reports are related to the consumed materials and parts and present them to the stakeholders.
4- Feedback
Finally, Material & Spare Parts Management affects these quantitative and qualitative reports to provide feedback for future planning.
10 Functional Steps of Pre-Overhaul Phase in Materials and Spare Parts Management in a Refinery
As we promised earlier, in this section of the article we are going to explain an important process. We give a detailed description of the steps of the first phase. As you remember, it was about Materials & Spare Parts Management in the pre-overhaul phase in the refinery. This process consists of 12 main steps:
1- Listing and Identifying all Spare Parts
2- Classification
3- Issue and Manage the Bill Of Materials (BOM)
4- Documentation of Work Orders
5- Access Limitation to the Warehouse Inventory
6- Optimize the Warehouse, Follow-up & Monitoring
7- Use Computerized Systems to Inventory Control
8- Allocate Stock Location for Spare Parts
9- Implement Following-up the Supply Processes Periodically for the Shortage of Inventory
10- Submit Reports to Stakeholders Periodically in Overhaul Coordination Meetings
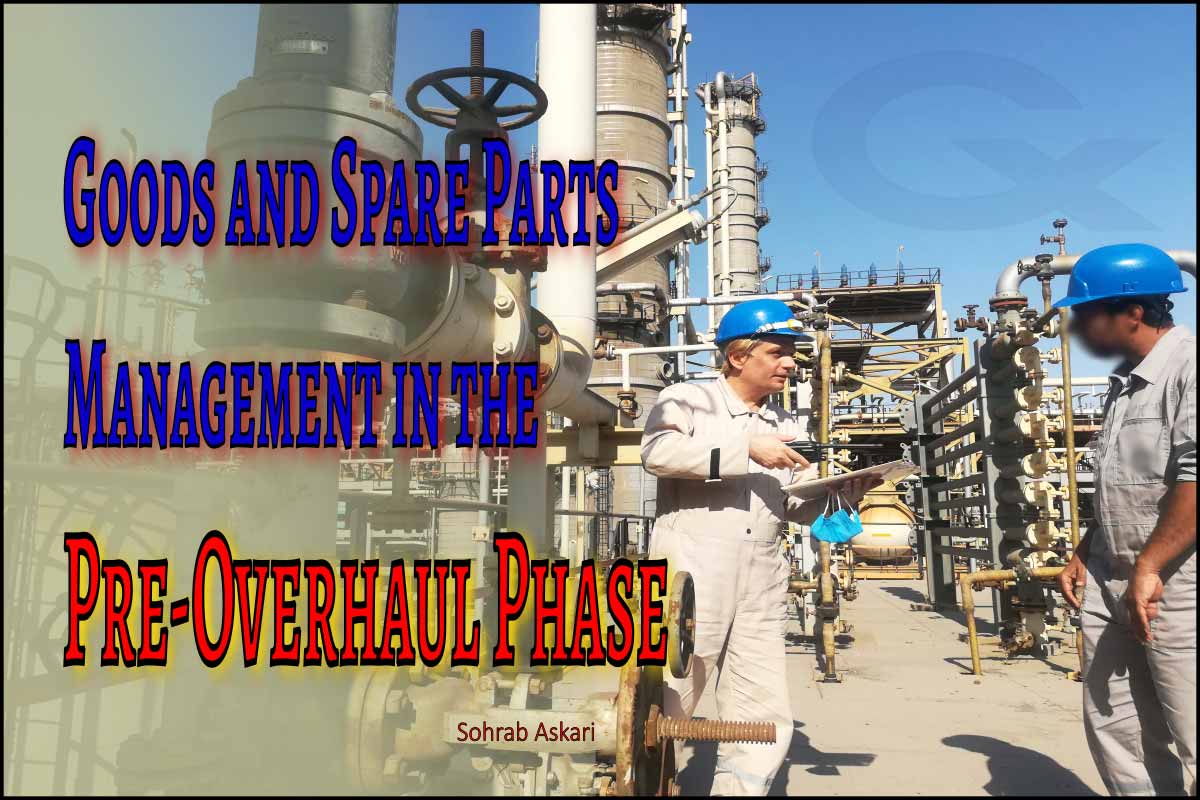
1- Listing and Identifying all Spare Parts
By listing all the items and parts in the equipment and machinery, we will have a comprehensive databank of the parts. In the next steps, this databank can be used to make an estimation of required parts for the overhaul and save needed parts in stock. By this databank also It will be possible to provide a real shortage-list of parts which are NIS (Not In Stock). After comparison with stock inventory, to initiation supply processes till provide them.
Also, having these two data helps us to be able to add them to stock after the overhaul:
- A database of parts that were in the equipment before the Overhaul.
- A list of other parts that were purchased for the Overhaul but not used during the overhaul.
These items must be added to the inventory control system and placed in the component inventory in the EAMS / CMMS. Other equipment in the refinery may be able to use similar parts or in the next Overhaul, it can be used
2- Classification
Classifying the materials and spare parts as per criticality helps to make an effective & safe stock. The classification should be done as them critical values. These lead to having good availability in time with the lowest cost at the minimum inventory value.
3- Issue and Manage the Bill Of Materials (BOM)
Bill of Materials (BOM) is documental order used for the prediction of planned spare parts requirements for management of overhaul in the refinery.
After two steps before, the Materials and Spare Parts Management sends a list to the Procurement Management. The list includes all the items needed to carry out the overhaul. These items are spare parts that have MESC (Material & Equipment Standard Code).
The Procurement Manager receives BOM documents. Then he performs the relevant analyzes and stores the items available in the warehouse for the Overhaul. For items that are inventory shortages in the warehouse, the process of the supply (purchase or build) starts based on the issued requisition forms.
It is worth noting that the MESC (Material & Equipment Standard Code) is created only for items in the warehouse which has a regular and iterative consumption in the specified period of time. In fact, for items that have no iterative consumption in the period of time, MESC isn’t created. It is in order to reduce the costs associated with the warehouse.
For this category of items, the Materials and Spare Parts Management directly sends purchase or build requisition to the Procurement Management. This process leads to the start of the supply process.
As later will be said, one of the tasks of Materials and Spare Parts Management is monitoring the supply process and carrying out their relevant follow-up.
4- Documentation of Work Orders
Using this method, the reasons for storage or supply of requested items are determined. In addition, previous work orders that have been sent to PM moves to Overhaul and prevent rework.
5- Access Limitation to the Warehouse Inventory
Making an access limitation to the warehouse inventory is mandatory to keep inventory accuracy for Overhaul. According to this policy, only determined employees have access to entry and exit points. Allowing everyone to have access can cause quickly decrease material and spare parts due to free consumption.
6- Optimize the Warehouse, Follow-up & Monitoring
You can make security easier by a potential control on the inventory accuracy. It will be possible via:
- Optimizing the Warehouse.
- Regular Follow-up.
- Inventory Monitoring.
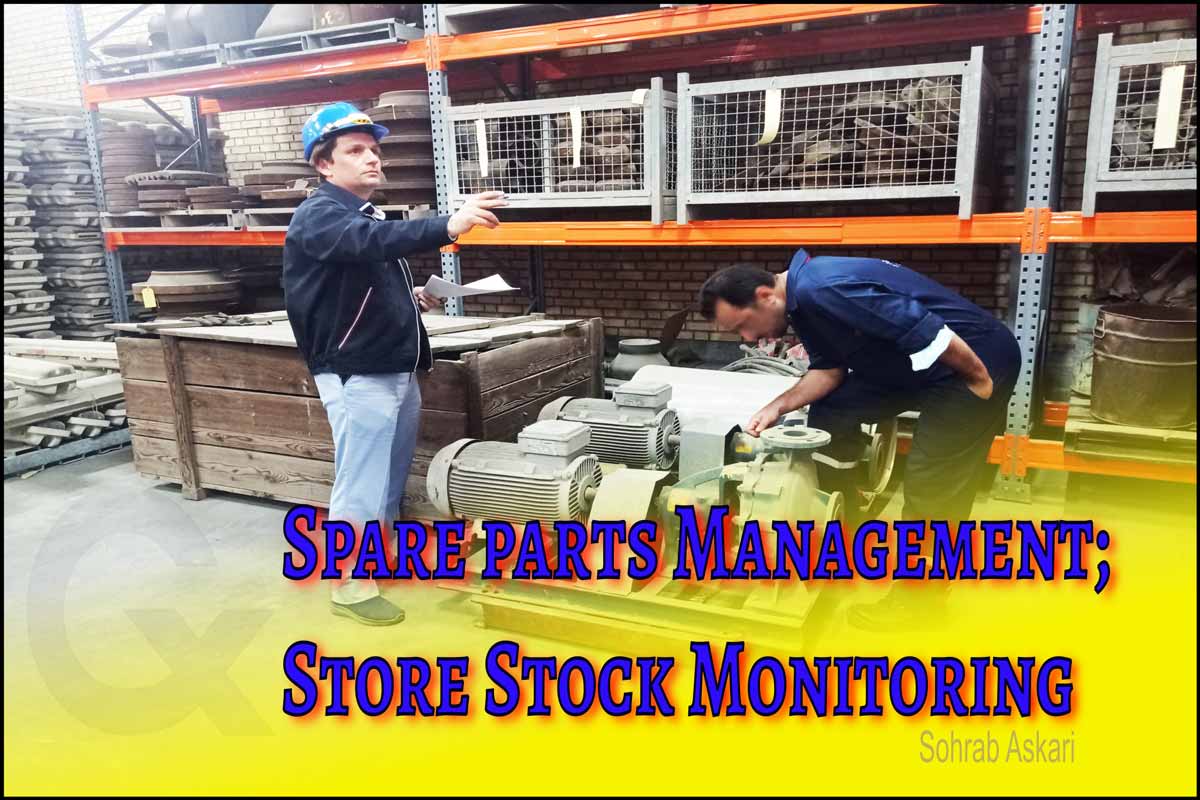
7- Use Computerized Systems to Inventory Control
Materials and Spare Parts Management uses a Warehouse Management System (WMS). It is a comprehensive application for warehouse management. It helps perform all functions related to monitoring the inventory.
These systems are connected to CMMS (Computerized Maintenance Management System) and EAM (Enterprise Asset Management). Materials and Spare Parts Management in a refinery applies these systems. It’s because of monitoring all the logistical processes related to consumption more accurately and easily.
8- Allocate Stock Location for Spare Parts
Materials and Spare Parts Management can assist the Logistics Management in location-allocation of the storage of the requested spare parts (needed for Overhaul). It must also make sure that these warehouses are created with the least complexity and the clearest detail.
9- Implement Following-up the Supply Processes Periodically for the Shortage of Inventory
One of our requirement is performing a periodical control on shortage of inventory and monitoring the supply processes regularly. It causes more coordination between Maintenance Management & Logistics Management. This following-up surely leads to providing the required spare parts in time.
10- Submit Reports to Stakeholders Periodically in Overhaul Coordination Meetings
Materials and Spare Parts Management analyzes all information about the last status of the spare parts shortage and the related supply processes. It presents the results periodically in the form of managerial reports at the Overhaul coordination meetings.
This makes it clear that we are at which point in the progress of the procurement process. It causes more coordination between the logistics and overhaul-related Overhaul project team members.
This process also exposes new challenges and clears the distance to the ideal point for Overhaul stakeholders. It helps stakeholders, logistics managers, and maintenance managers together make new decisions and find better solutions to logistical problems.
Benefits of Materials and Spare Parts Management in the Refinery
Obviously, powerful material management has an important role in the implementation of repair projects. He especially in Overhaul can make the difference between having spare parts when needed and spending a lot of time and money supplying them emergencies in very sensitive situations. This makes Materials and Spare Parts Management a key and strategic role in the planning of Overhaul projects.
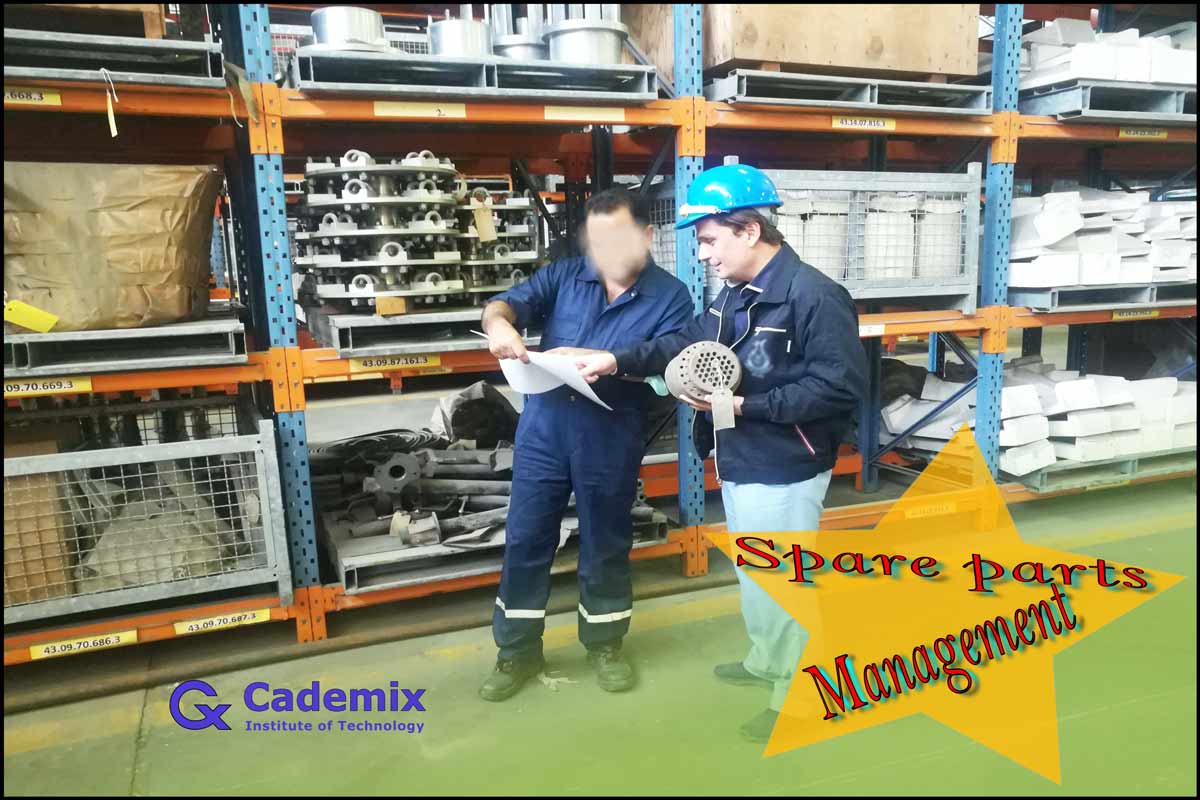
Materials and spare Parts Management leads to having a good and responsible inventory system. It also makes a logical availability of needed spare parts for Maintenance projects. It provides an agile reliable stream to help Logistics Management and Supply Chain Management (SCM).
so, the benefits of having effective Materials and Spare Parts Management includes:
- Ensuring availability of needed materials & spare parts.
- Reduced delays on SCM stream and flow.
- Reduced inventory costs.
- Working capital improvement.
- Increased safety.
- Improved Risk Control of business operations.
- Total cost optimization by decrease equipment downtime and production stops.
Keywords Related to Materials and Spare Parts Management in Petroleum Oil Refinery
Major keywords related to Materials and Spare Parts Management in refineries are:
Materials and Spare Parts Management, in refineries, Spare Parts Management, Procurement, Spare Parts, Oil refinery, Refinery, gasoline, Spare Parts, CMMS software, MESC, Spare Parts Management, Materials, Oil industry, Overhaul, Maintenance. Then, Materials, Spare Parts Management in Maintenance, Spare Parts, Overhaul, warehouse, Inventory, Bill of Materials, BOM, Pre-overhaul, Post-overhaul.
Other Keyphrases related to Materials and Spare Parts Management in refineries include: Procurement, Emergency Maintenance, EM, Corrective Maintenance, CM, Preventive Maintenance, PM, Predictive Maintenance, PDM, Emergency Maintenance, Planned Maintenance, PM, gasoline, Spare Parts.
Further, we can mention crude oil, vessel, ship, delivery, refineries, kerosene, Spare Parts, maintenance, Crude Oil, Petroleum industry, Gases, Boiling, Hydrogen-sulfide, Spare Parts Management, Residual, Sulfide, Refining industry, Fluid catalytic cracking, Oil-company, Oil companies, Isomerization, Sulfuric-acid, Sulfuric, Butane, Process safety, Spare Parts Management in Maintenance,
About the Author
Sohrab Askari is an associate Multidisciplinary Engineer at Cademix Institute of Technology (Austria). He studied MSc in Industrial Engineering and BS in Computer Engineering. Mr. Askari has Multidisciplinary skills in Supply Chain Management (SCM), Project Management, several Computer Programming Languages, and Mechatronics. He has also worked in a large refining company with a global reputation for several years (more than 15 years) in the field of Supply Chain Management (SCM) and Project Management of maintenance focused on Oil industries especially Oil refining companies.
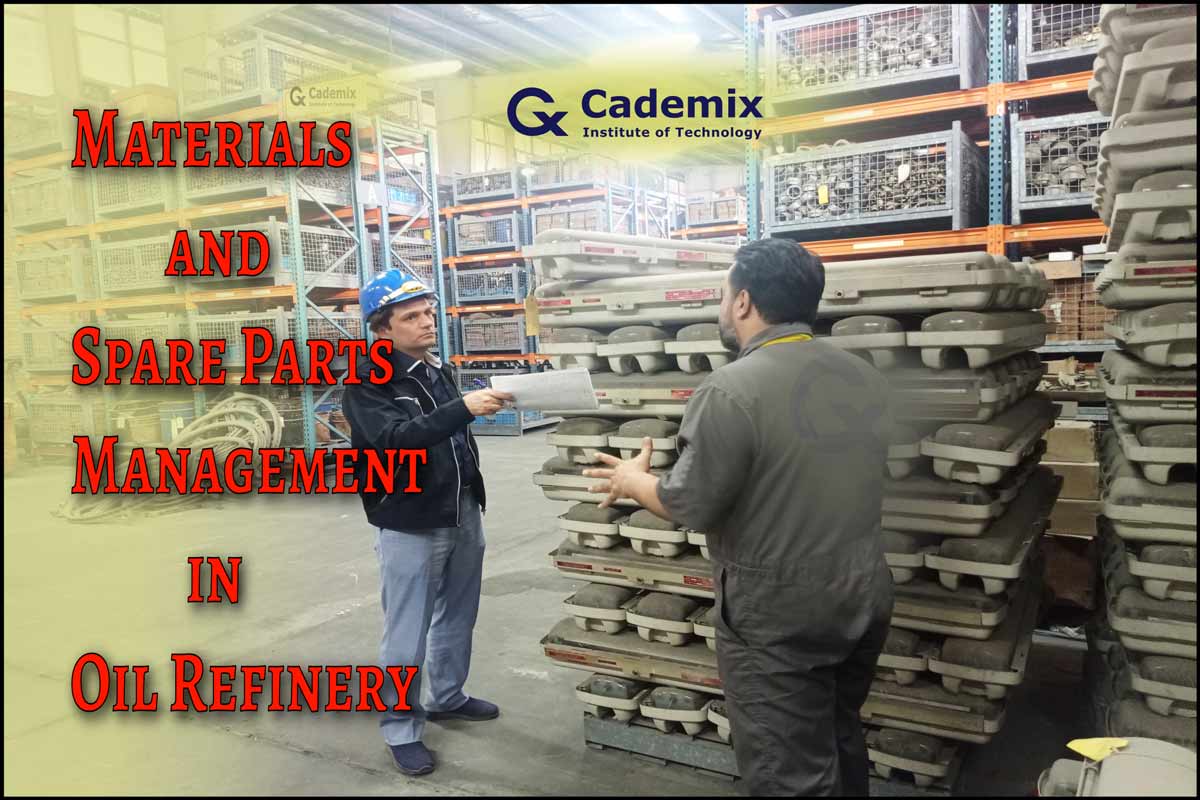