In this article, we review the skills for material engineers. The Industries hire engineers who have technical skills such as failure analysis, data analysis, as well as other skills such as management skills, soft skills and a lot more. This magazine article targets public awareness and early career investigators.
By: Akashy Toradmal, Cademix Institute of Technology
Introduction
The industries look for engineers, who can work alongside design and manufacturing teams on material-related issues. This is where materials engineers come into play, who deal with the extraction, processing, testing, and development of materials. These stages define the basis of product and technological development in the field of industries such as aerospace, oil & gas, automotive, and medicine. Therefore, one could say that the material engineers lay the foundation for the success of the organization. Each of those stages could demand a combination of soft and hard skills that engineers should possess to meet the challenges in those stages. Material engineers can imbibe these skills during various stages of education and profession. This article gives a brief overview of the skills for material engineers in order to be successful in the workplace.
What are the credentials of a materials engineer?
The materials are broadly classified into 4 types: metals & alloys, ceramics, polymeric and composite materials. Therefore, the materials engineer should acquire knowledge of these materials through education and training. The academic engineering program during bachelors and masters introduce an aspiring material engineer to the various fields of metallurgy & materials engineering. Concurrently, laboratory experiments and industrial internships help comprehend the concepts better. When a person starts to work as a materials engineer after graduation, the person learns about the know-how to run an organization. During various stages of education and profession in the materials engineering field, an individual develop some or all of the following skills.
Laboratory skills
The material engineers are responsible for planning and execution of tests, analysis of test results and their documentation. At the same time, they are responsible for all the equipment in the laboratory, their maintenance, and calibration. There are a number of testing methods to determine the different properties of the materials. The determination of these properties decides the suitability of a material for a specific application. The properties of the materials are broadly categorized into two groups: physical properties and chemical properties.
Physical properties
The physical properties include mechanical, electrical, magnetic, optical, and thermal properties of the material. The mechanical testing methods determine the mechanical properties of materials. They are most widely used across various industries to ensure safety, to design cost-effective components and to develop new engineering materials.
Destructive and non-destructive testing methods
According to the Handbook of Materials Measurement Methods, One of the most demanding skills for material engineers is the know-how and interpretation of these test methods. Many components fail under the application of load during their service. Therefore, it is necessary to evaluate the response of the material to the different types of loads before finalizing it for the specific application. The following Table 1 summarizes the typical tests and properties determined by them.,
Testing method | Property/Properties |
Tensile Test | Stiffness, Elasticity, Ductility, Yield and Tensile strength, Fracture stress, modulus of toughness |
Brinell, Rockwell, Vickers | Hardness |
Impact Test | Toughness |
Creep Test | Creep Behaviour |
Wöhler Fatigue Test | Fatigue Strength |
These test methods are destructive testing methods, as the specimen is loaded until its failure and can no longer be used for an application. In addition to these methods, there are Non-Destructive Testing (NDT) methods. Engineers use these methods to evaluate the properties of a material, component or structure without destroying their serviceability. Many a time, it is necessary to assess the damage state of the equipment or component without shutting down plant operations. As a result, the engineers use NDT methods to assess the damaged state of the equipment by detecting the defects and flaws to ensure the safe and stable functioning of the materials. The following picture depicts one of the NDT methods, the visual inspection method, to detect cracks, porosities or pits on the surface of the component.
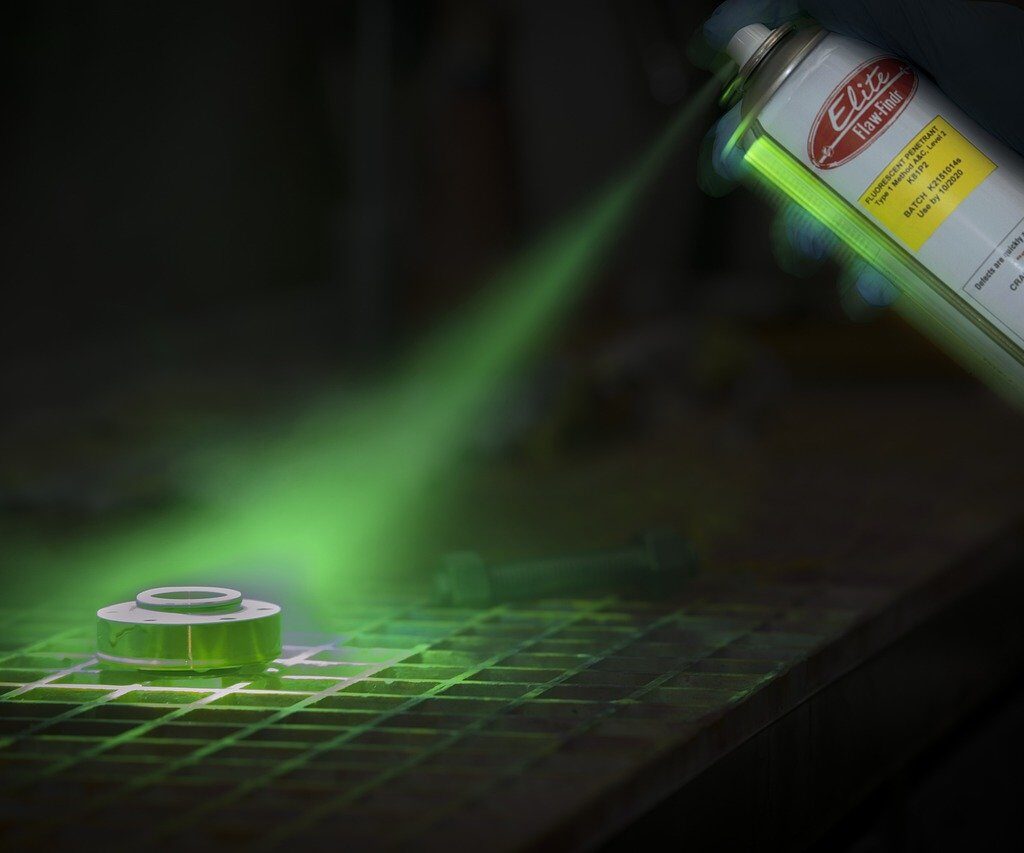
Tribological testing methods
Tribological testing represents an important part of mechanical test methods. Some components of the machine operate by rubbing together. Tribology is the science and engineering of such interacting surfaces in relative motion, which encompasses the research and application of friction, lubrication, and wear concepts. As a result of friction and wear between these contacting surfaces, components could either fail or reduce the efficiency of the machine. Moreover, friction and wear have a negative impact on energy consumption, economic expenditure, and CO2 emissions. So, engineers tackle this problem by evaluating the component-specific tribological properties such as wear, friction, adhesion etc. and then taking the decisions regarding the selection of materials, optimisation of process parameters, surface treatment/coating, and appropriate lubrication. These properties are determined by means of tribological tests such as pin on disc, four-ball test, or Taber test.
Chemical properties
Properties of materials, such as flammability, toxicity, and ability to corrode change by virtue of their chemical reaction with the environment. Corrosion of materials is one of the most significant problems in a variety of industries. According to the NACE’s report, the total estimated cost of corrosion across the globe in 2013 was astronomical i.e., 3-3.4% of the global GDP. So, to cut down this cost and to prevent dangerous consequences of corrosion, industries require an interdisciplinary approach of the materials engineer, the chemist, and the designer. The materials engineer should be in a position to recognize different forms of corrosion and parameters to avoid or mitigate the corrosion. Additionally, they should possess corrosion testing skills to estimate the material life, compare the performance of materials in an environment, and assess the suitability of materials under actual conditions. These tests include potentiodynamic polarization test, cyclic voltammetry, salt spray test etc.
Metallographic examinations skills
One of the most common skills for material engineers is the ability to conduct metallographic examinations. The constituents of the microstructure determine the properties of the material. Therefore, material engineers need to observe the microstructure at various stages of their work. The microstructures are observed by means of different types of microscopes. Prior to the microscopic investigation, the material has to be prepared in several stages. These stages are as follows:
- Cutting
- Mounting
- Grinding
- Polishing
- Etching
Stages 1-5 along with the microscopic observations fall under the term “Metallographic Examinations”. Depending on the microscopy techniques, a sample may go through all or some or none of these preparation steps. Some of the most widely used microscopes are Light Optical Microscopy (LOM), Scanning Electron Microscopy (SEM), and Transmission Electron Microscopy (TEM) etc. The material engineers should possess theoretical knowledge and know-how of these microscopic methods, so that they can plan and execute the metallographic examinations as per the requirement.
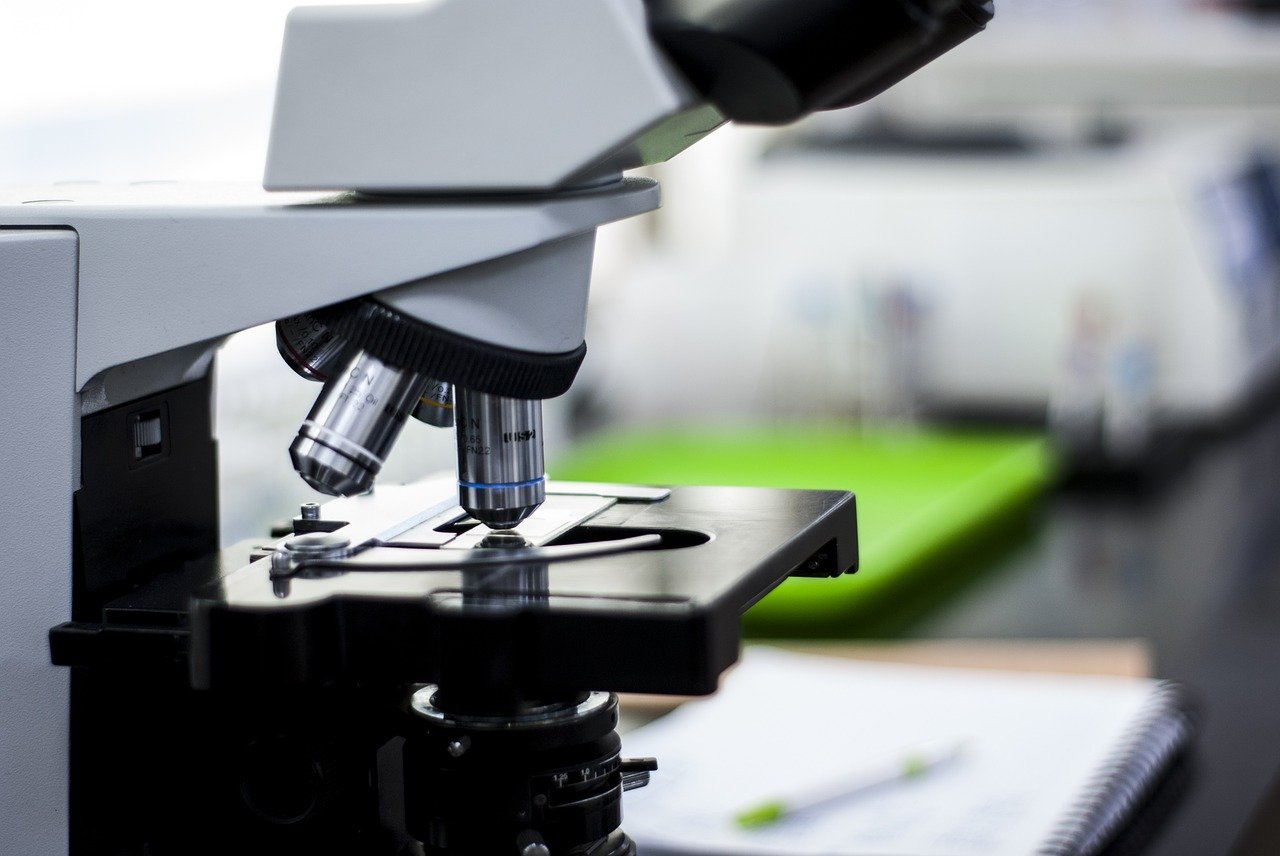
Failure analysis
This is one of the most valuable skills for material engineers because it takes years to develop this skill. Failure analysis is the science and technique of understanding, examining, and identifying the underlying causes of material failures. The failure analysis helps in preventing further damage to the component. In order to carry out the failure analysis, engineers must be cognizant of the following factors:
- Material making processes
- Metal working or fabrication processes and related defects
- Type of loading to which a part was subjected or their combination
- Characterization techniques for the different types of investigations
- Literature research
In short, a materials engineer has to use all of his/her knowledge and experience about a wide gamut of fields in materials and metallurgical engineering to carry out failure analysis.
Data Analysis
Every engineer must be conversant with the handling of data. Specifically, it means that they should be able to extract valuable information and solve a problem. For instance, material engineers need to analyse the numerical data after conducting the tests on the materials. So, to analyse this data, it has to be represented in the form of curves, bar diagrams, pie charts etc. The following figure shows the various diagrams of data representation. An engineer can use software like Microsoft Excel, Origin, Python, and MATLAB to accomplish these tasks. The application of these software in the context of materials engineering is one of the interesting skills for material engineers.
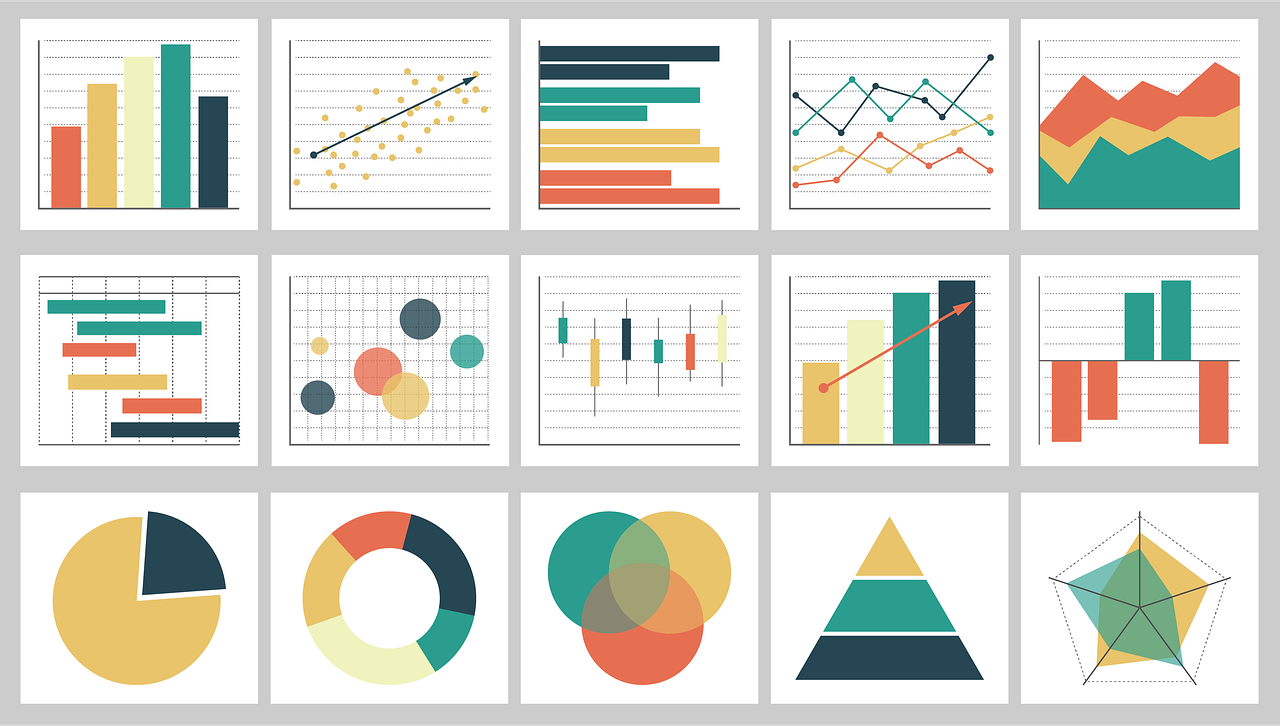
Material modelling and simulation
Simulation has emerged as one of the most sought-after skills for material engineers in recent years. Many organisations adopt this approach for rapid material and process development because it can save time, money, and resources. Simulation is a process of using a model to study the behaviour and performance of an actual or theoretical system. The material engineers should develop this skill to predict the properties of the materials and then decide the necessary steps to influence future behaviour. This analysis can be done using software such as Simulink, COMSOL, and ABAQUS.
Process improvement Tools
Materials engineers may work in manufacturing industries, wherein they are responsible for process improvement as well as quality improvement. Specifically, KAIZEN, LEAN and Six Sigma are amongst the most widely used methodologies/concepts in the industrial sectors. They focus mainly on process improvement and quality improvement. Therefore, material engineers should participate in the training courses of KAIZEN, LEAN, and Six Sigma. Then, they should try to integrate their principles in an organization to bring about operational excellence for business excellence.
Interpersonal skills
Material engineers may work on more than one project task at a time. During this process, they come across suppliers, customers, team members, superiors, juniors, and cross-functional teams. Therefore, an engineer must have interpersonal skills to express himself in front of persons of varied interests. Interpersonal skills are the traits that one possesses to interact and communicate with individuals and groups. There are a number of interpersonal skills, most of which depend on the organization. Employers are always looking for engineers with interpersonal skills such as communication skills, team player, leadership skills, problem-solving skills, time management skills etc. So, let’s discuss some of these skills briefly.
- Communication skills: Firstly, good communication skills allow individuals to convey their thoughts and information more accurately and quickly. Secondly, these skills can deepen the relations in personal and professional life. Moreover, according to the survey conducted by LinkedIn in 2016, communication skill is the most in-demand soft skills by employers.
- Problem solving skills: The engineers need to step up in an unexpected or difficult to handle situations with level-headedness and resilience. They need to identify the underlying problem and then implement a solution.
- Time management skills: Engineers must follow a timeline to complete the tasks and utilize their time effectively. They can achieve it by goal setting, organization, planning and prioritization of tasks, and stress management.
- Team player: Employees must commit themselves to ensure that their team succeeds with all tasks, duties, and projects. To achieve this objective, an engineer should help team members, respect their opinions, and resolve a conflict by fairly listening to both sides. These are also the qualities of an ideal team player. Therefore, employers prefer team players over egoistic, self-centred, and impatient employees. Moreover, team players maximize the work productivity and contribute to the growth of the organization.
What if you miss an skill?
No one is perfect, and you may not always fulfil all the criteria of the industries. For instance, if you are a fresh graduate, you may need career improvement. So, there is always some sort of career gap or skill gap. The Career Autopilot Program of Cademix Institute of Technology intends to bridge this gap.
Related Keywords
Hard and soft skills, alloy, Characterization techniques, metallurgist, Material properties, Laboratories, elastic, minerals, deformation, ductile, brittle, Stresses, biomaterials, electron-microscope, Ceramics, Skills for material engineering, materials testing, materials technology, material-science, engineering research, Steels, Graphene, Thin film, thermodynamics, seminar, skillset, career, soft skills, career choices, Resume, CV, training, skills improvements.